How Much Does A Resin Garage Floor Cost
Are you considering upgrading your garage floor to a resin finish but unsure about the cost and installation process?
We will explore the benefits of a resin garage floor, the steps involved in the installation, factors that affect the cost, and how to choose the right contractor for the job.
Stay tuned to learn more about the average cost of a resin garage floor, factors that can increase the cost, and whether it’s worth the investment.
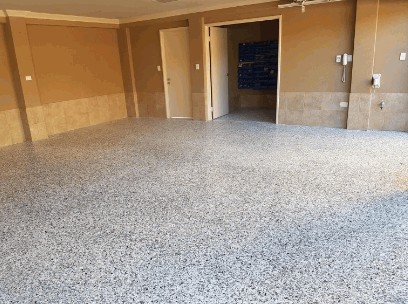
What Is A Resin Garage Floor?
A resin garage floor is a type of flooring system that uses resin-based materials to provide a durable and attractive surface for garage spaces. Resin floors are known for their strength, chemical resistance, and customizable designs.
These flooring systems offer a seamless and non-porous surface, making them easy to clean and maintain. With epoxy coatings, resin garage floors are not only aesthetically pleasing but also highly resistant to stains, impacts, and water damage. The various types of resins used in garage flooring range from polyurethane to methyl methacrylate, each with its unique properties suited for different surfaces and levels of use. When applied correctly, resin flooring can significantly enhance the durability and longevity of your garage floor.
Take a look: Does Epoxy Flooring Increase Home Value
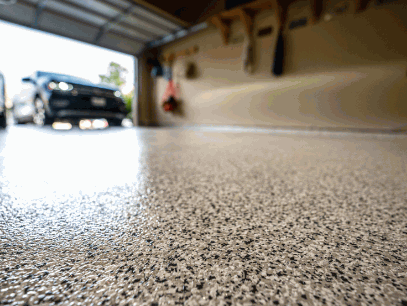
Why Choose A Resin Garage Floor?
There are several reasons to choose a resin garage floor over other flooring options. Epoxy garage floors offer durability, easy maintenance, and a wide range of design options to enhance the aesthetic appeal of your garage.
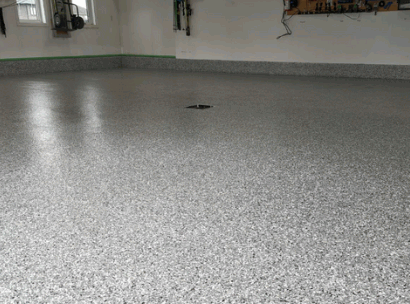
How Is A Resin Garage Floor Installed?
Installing a resin garage floor involves meticulous preparation, precise application of the resin coating, and thorough curing for a long-lasting finish. While some homeowners opt for a DIY approach, hiring a professional ensures a seamless installation.
Preparation Of The Existing Floor
Before applying a resin coating, preparing the existing garage floor is crucial. This involves thorough cleaning, repairing any damages, and ensuring a smooth surface for the resin to adhere to.
For a successful garage floor installation, proper surface preparation not only ensures the longevity of the coating but also enhances the overall aesthetics of the space. Cleaning the floor is the initial step, as it removes dirt, grease, and previous coatings that can interfere with the new resin. Repairs are essential to fix cracks or uneven areas, preventing them from compromising the final result. A clean and dry surface is vital in achieving a strong bond between the resin and the floor, minimizing the risk of peeling or chipping over time.
Application Of The Resin Coating
The application of the resin coating requires precision and expertise to ensure a uniform and durable finish. Whether using a roller, squeegee, or sprayer, the goal is to achieve a seamless coating that enhances the garage floor’s appearance and performance.
Rolling the resin coating is a common method that provides good coverage and control over the application process. It is ideal for smaller garage floors and allows for easy maneuvering around obstacles.
Squeegeeing is another technique that works well for larger areas, ensuring a smooth and even finish. This method requires steady hand movements to distribute the resin evenly without leaving any patches.
For larger garage floors, using a sprayer can be efficient, covering larger areas quickly. Precision is crucial to avoid overspray and ensure even application.
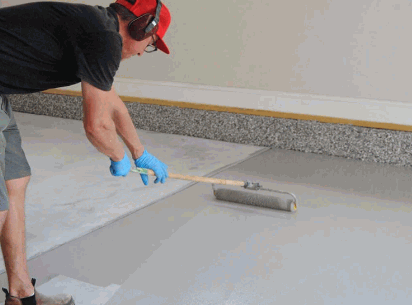
Curing And Finishing Touches
After the resin coating is applied, allowing sufficient time for curing is essential to ensure the durability and longevity of the garage floor. Finishing touches like adding a topcoat for extra protection can further enhance the resilience of the flooring.
During the curing process, various factors can impact the outcome, affecting the overall quality of the floor. Factors such as temperature, humidity levels, and proper ventilation play crucial roles in allowing the resin to be set correctly.
High humidity or extreme temperatures can lead to improper curing, resulting in a weaker finish. Therefore, it is important to monitor these conditions closely during the curing phase to achieve optimal results.
What Factors Affect The Cost Of A Resin Garage Floor?
Several factors influence the cost of installing a resin garage floor, including the size of the garage, the type of resin used, the condition of the existing floor, and any additional features or customizations desired.
Garage size plays a significant role in determining the overall cost, as larger garages require more materials and labor. The choice of resin type is crucial, with epoxy being a popular and durable option that comes with varying price points based on quality.
Existing floor conditions can also impact costs, as repairs or preparations may be necessary before applying the resin coating. The level of customization, such as patterns, colors, or textures, can add to the final price.
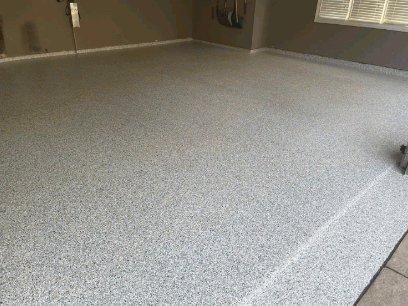
Size Of The Garage
The size of the garage directly impacts the overall cost of a resin floor installation. Larger garages require more materials and labor, resulting in higher installation expenses compared to smaller spaces.
When undertaking a resin flooring project for a garage, it’s essential to consider the square footage of the space as a major cost factor. A larger garage means there is a need for more epoxy resin and other materials to cover the extended surface area. The labor costs are likely to increase with larger garages as more time and effort are required to complete the job.
Type Of Resin Used
The choice of resin type significantly affects the total cost of a garage floor installation. Different epoxy formulations, such as water-based or solvent-based resins, come with varying price points and performance characteristics.
Water-based epoxies are generally more cost-effective upfront, making them an attractive option for budget-conscious individuals. They also tend to have lower VOC emissions, making them environmentally friendly.
On the other hand, solvent-based epoxies are known for their durability and resistance to chemicals and abrasions, which may justify their higher initial cost. Solvent-based formulations can be more challenging to work with due to stronger fumes and longer curing times, impacting installation costs.
Condition Of The Existing Floor
The condition of the existing garage floor can influence the overall cost of installing a resin floor. Floors in poor condition may require repairs or additional preparation, adding to the total project cost.
Assessing the state of the current garage flooring before installing resin not only impacts the financial aspect but also ensures a smooth and durable outcome. Evaluating the floor condition meticulously can reveal underlying issues such as cracks, uneven surfaces, or moisture problems that need to be addressed beforehand. These necessary repairs and surface treatments not only prolong the lifespan of the new resin floor but also prevent future maintenance costs.
Additional Features Or Customizations
Opting for additional features or customizations, such as decorative patterns or color options, can increase the overall cost of a resin garage floor project. These enhancements add aesthetic value but come with supplementary expenses.
Custom features play a crucial role in elevating the appearance of the garage floor, transforming it from a basic surface to a visually appealing space. With this transformation comes an increase in costs as the customization process involves specialized materials and skilled labor. Unique design options, like intricate patterns and customized color schemes, can further escalate the project expenses, making it essential for homeowners to carefully consider the trade-offs between their desired features and the associated costs. While these custom features add a personalized touch, individuals must weigh the benefits against the financial implications to ensure a well-informed decision.
How Much Does A Resin Garage Floor Cost?
The average cost of installing a resin garage floor can vary based on several factors, including the size of the garage, the type of resin used, and any additional customizations. Understanding these cost components is crucial for budgeting your garage flooring project.
In terms of the national price ranges, you can expect to pay anywhere from $3 to $10 per square foot for resin garage floor installations. Factors such as the quality of the epoxy type, labor costs, and the complexity of the installation process all play a significant role in determining the overall expenses. Installation fees typically range from $2,000 to $6,000 for a standard two-car garage, but this can increase for larger spaces or if extensive prep work is required.
Average Cost Of A Resin Garage Floor
The average cost of a resin garage floor installation in standard homes falls within a national price range, considering factors like garage size, labor costs, and the type of resin selected. Obtaining quotes from contractors can provide a more accurate estimate for your specific project.
Garage size is a significant determinant of the overall cost, as larger garages require more materials and labor compared to smaller ones. Labor expenses play a crucial role, varying based on the expertise of the contractors and the complexity of the project.
The type of resin chosen can impact pricing; epoxy resin tends to be more cost-effective than polyurea, but it may offer different durability and aesthetic benefits. To ensure you get the best deal, it’s recommended to reach out to multiple contractors for quotes and compare costs before making a decision.
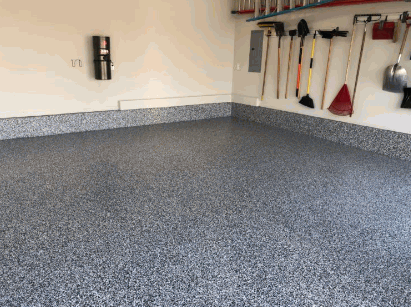
Factors That Can Increase The Cost
Several factors can escalate the cost of a resin garage floor project beyond the average estimates. Custom design features, intricate patterns, or extensive repairs and preparations are examples of elements that may increase the overall expenses.
Custom design features often involve intricate detailing that requires additional labor and specialized materials, adding a premium to the total cost. Similarly, incorporating intricate patterns into the resin floor design can lead to higher expenses due to the complexity of implementation.
Extensive repairs and preparations, such as fixing underlying structural issues or leveling the surface, can significantly raise the project costs. These unforeseen repairs often demand specialized skills and materials, driving up the overall budget.
Is A Resin Garage Floor Worth The Cost?
Deciding whether a resin garage floor is worth the cost involves weighing its benefits, such as durability and aesthetics, against potential drawbacks like slipperiness when wet. Understanding the pros and cons can help homeowners make an informed investment decision.
One of the key advantages of opting for a resin garage floor is its durability. These floors are highly resistant to stains, chemicals, and impacts, making them ideal for high-traffic areas like garages. Maintenance is a breeze with resin floors, as they are easy to clean and require minimal upkeep compared to other flooring options.
In terms of design, resin floors offer a plethora of options. Homeowners can choose from various colors, finishes, and even textured surfaces to suit their style preferences.
On the downside, some may find resin floors to be slippery when wet, which can be a safety concern. Maintaining a pristine look may require occasional resealing or touch-ups depending on the wear and tear.
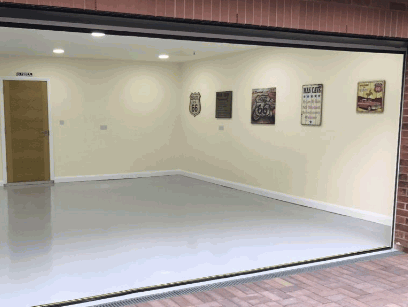
How To Choose The Right Contractor For Your Resin Garage Floor?
Selecting the right contractor for your resin garage floor installation is crucial to ensure a successful and high-quality outcome. Consider factors like experience, expertise, and customer reviews when choosing a professional contractor for your project.
Experience is key when it comes to resin garage floor installations. An experienced contractor has likely encountered various challenges and knows how to overcome them efficiently. Expertise in this specific type of flooring is essential to guarantee a flawless finish that meets your expectations. Prior client feedback can give you valuable insights into the contractor’s workmanship and professionalism.
It is advisable to get quotes from multiple contractors to compare prices and services offered. Checking references is vital to ensure that the contractor has a track record of delivering satisfactory results. Verifying credentials such as licenses and insurance coverage is also crucial to protect yourself in case of any unforeseen issues during the installation.